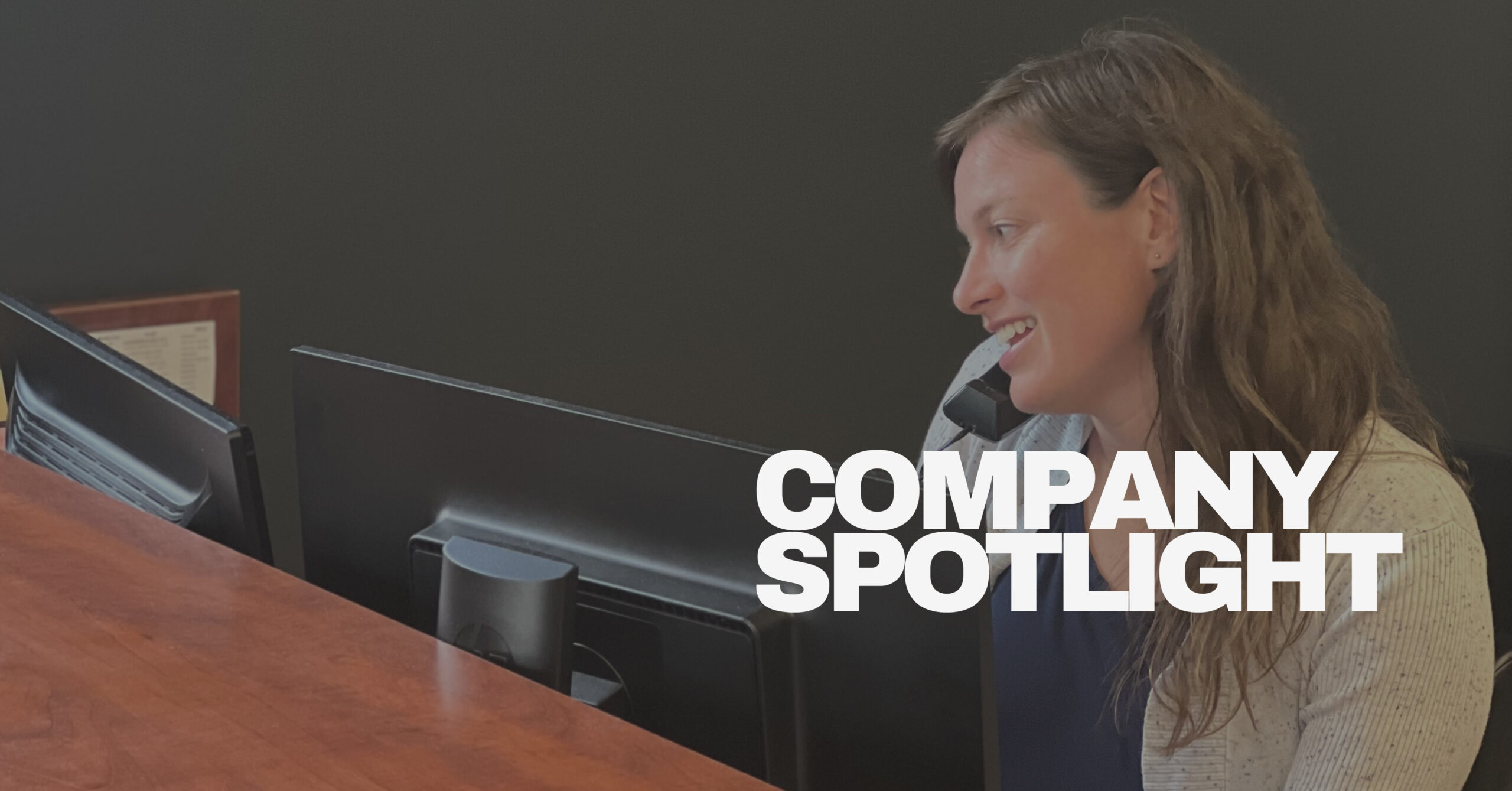
At TFG, we’re always looking for ways to better serve our customers. That’s why we’re excited to introduce...
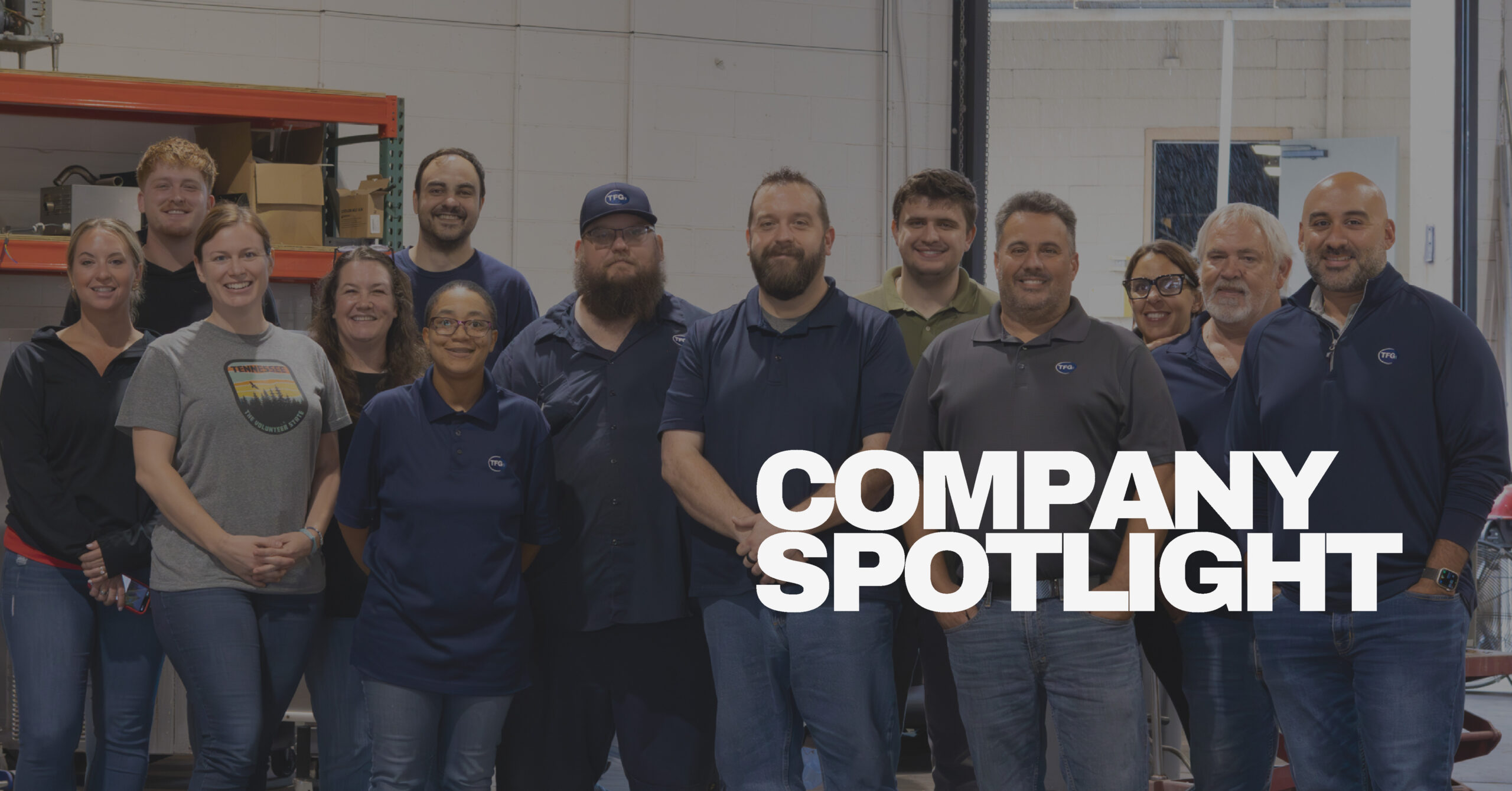
At TFG, we understand the importance of having trusted partners when operating in the foodservice industry,...
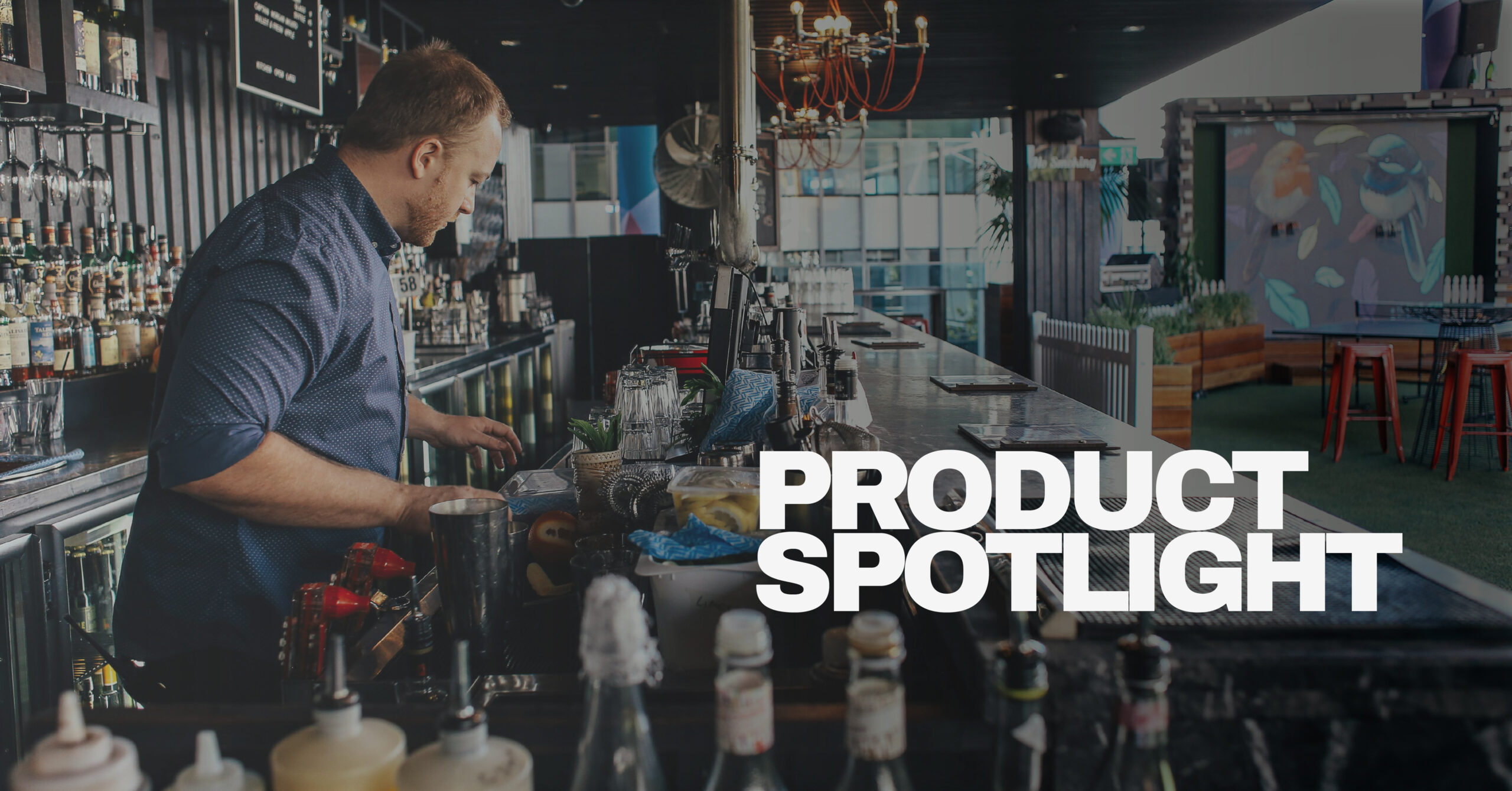
As temperatures rise, so does the demand for refreshing, cold beverages—and nothing says “patio season”...
![Blog Header Image [updtd]](https://tfgroupllc.com/wp-content/uploads/2025/04/Blog-Header-Image-updtd-scaled.jpg)
When it comes to maximizing efficiency in a busy kitchen, the control system on your fryer plays a big...
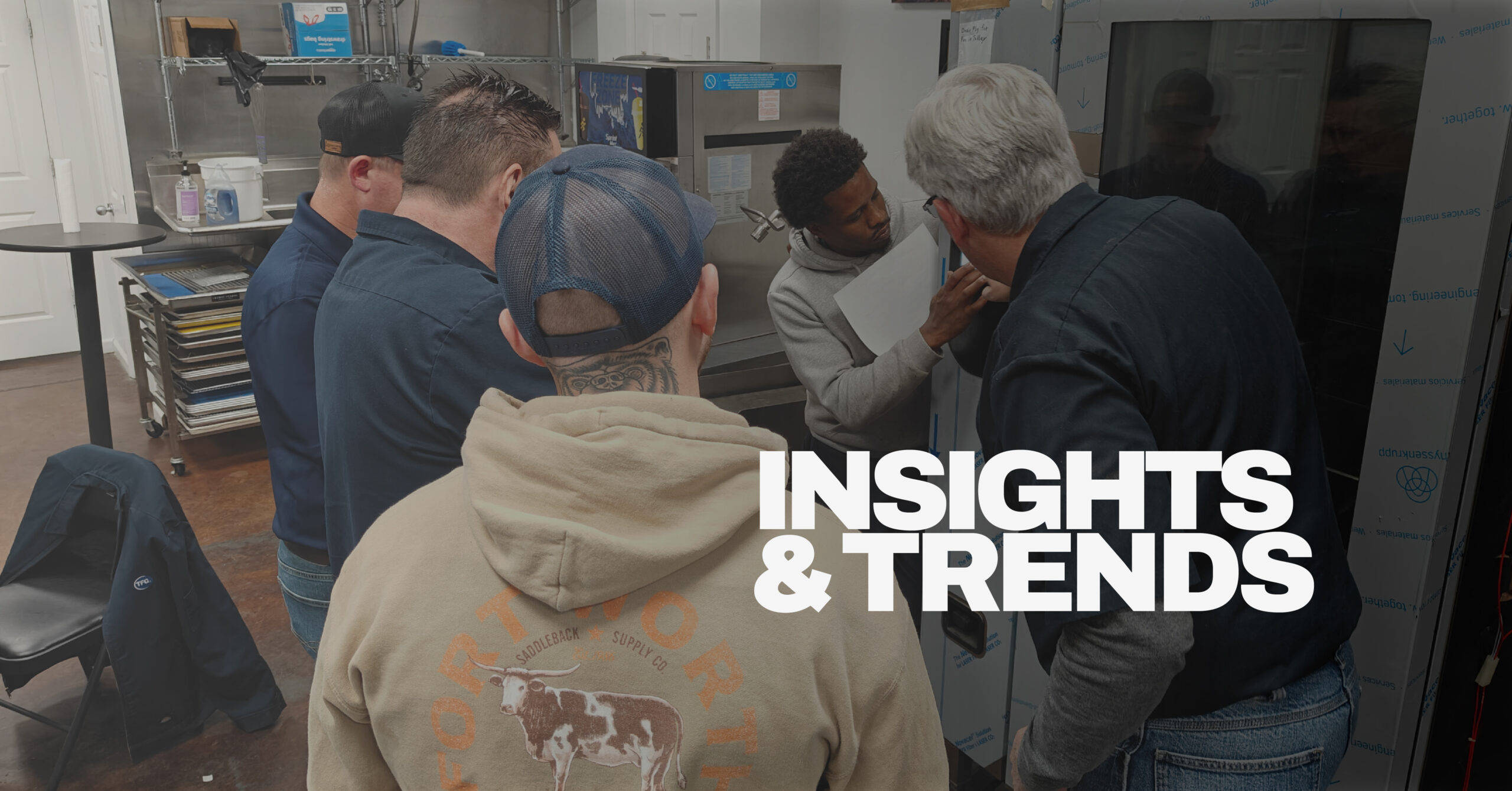
Investing in foodservice equipment is a big step toward running a successful kitchen, but the work doesn’t...
![Blog Header Image [z]](https://tfgroupllc.com/wp-content/uploads/2025/03/Blog-Header-Image-z-scaled.jpg)
In any commercial kitchen, fryer oil is a critical component of food quality, operational efficiency,...
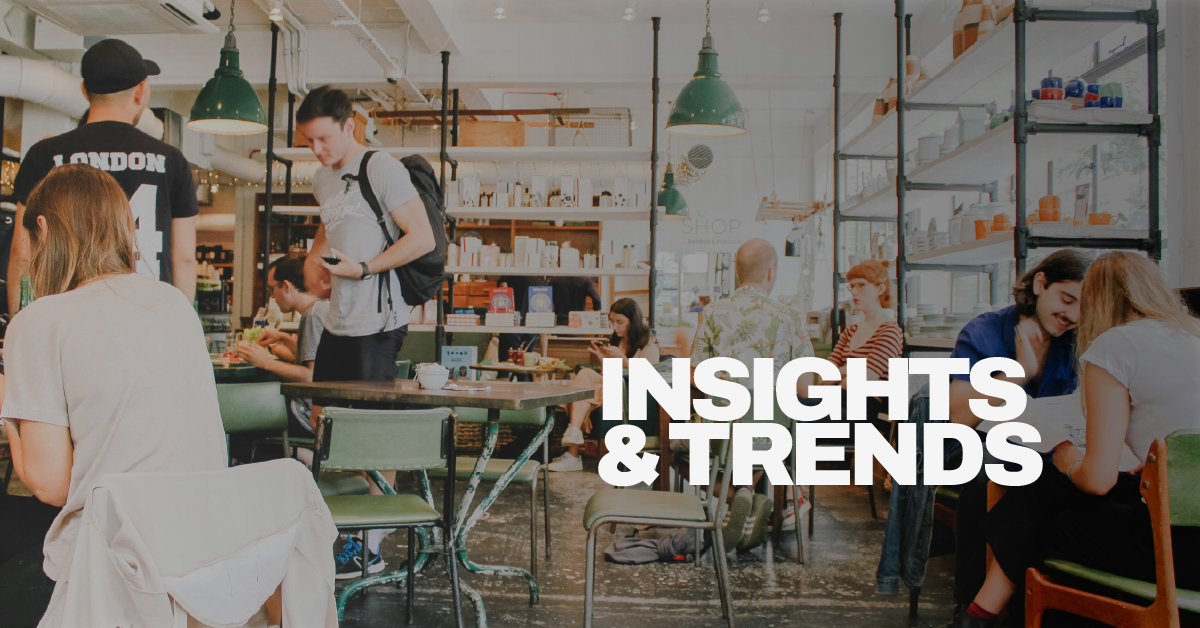
As 2024 draws to a close, the foodservice industry reflects on a year of transformation, innovation,...
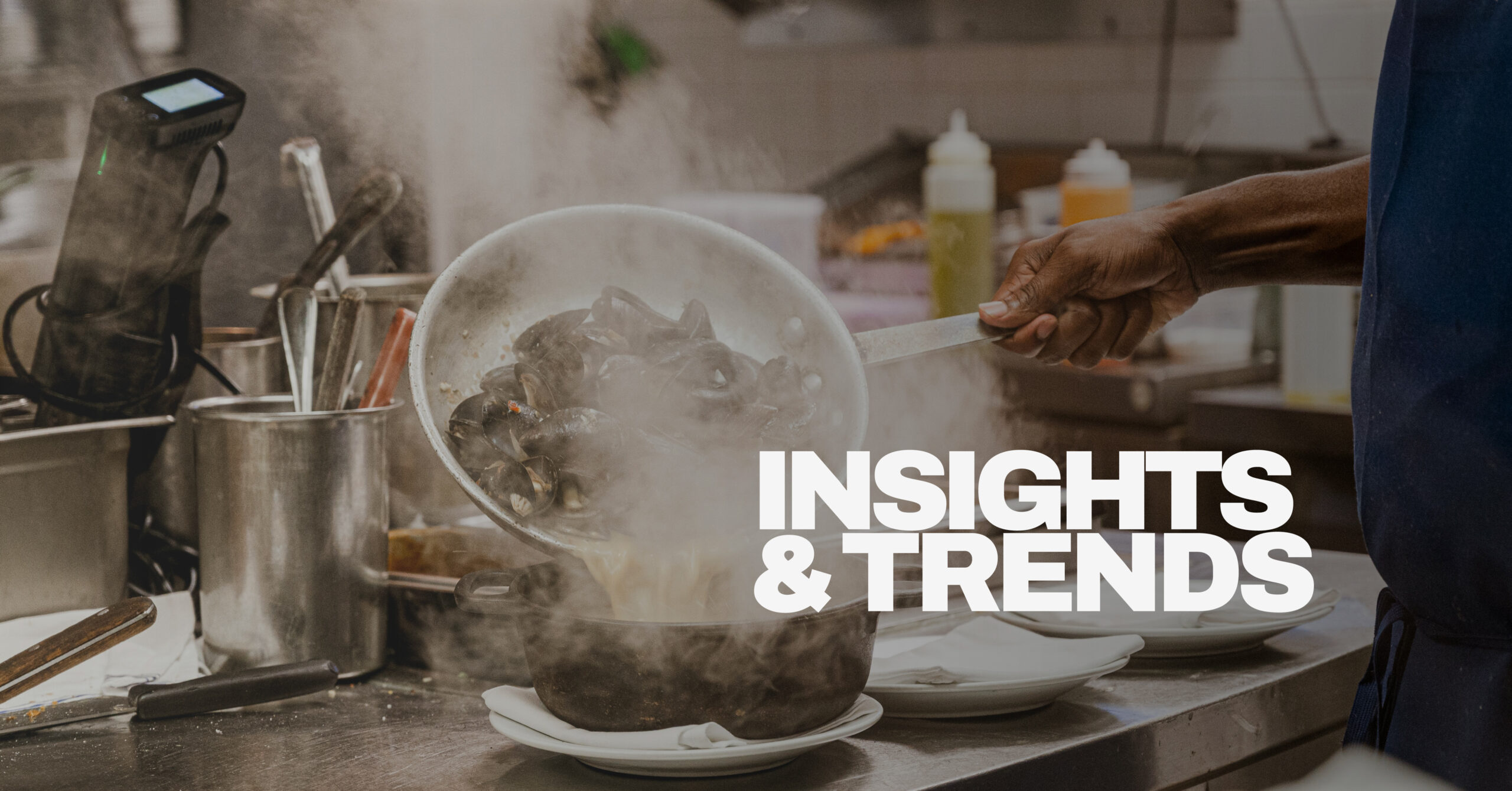
The holiday season is a busy (and often hectic) time for restaurant owners and foodservice operators....
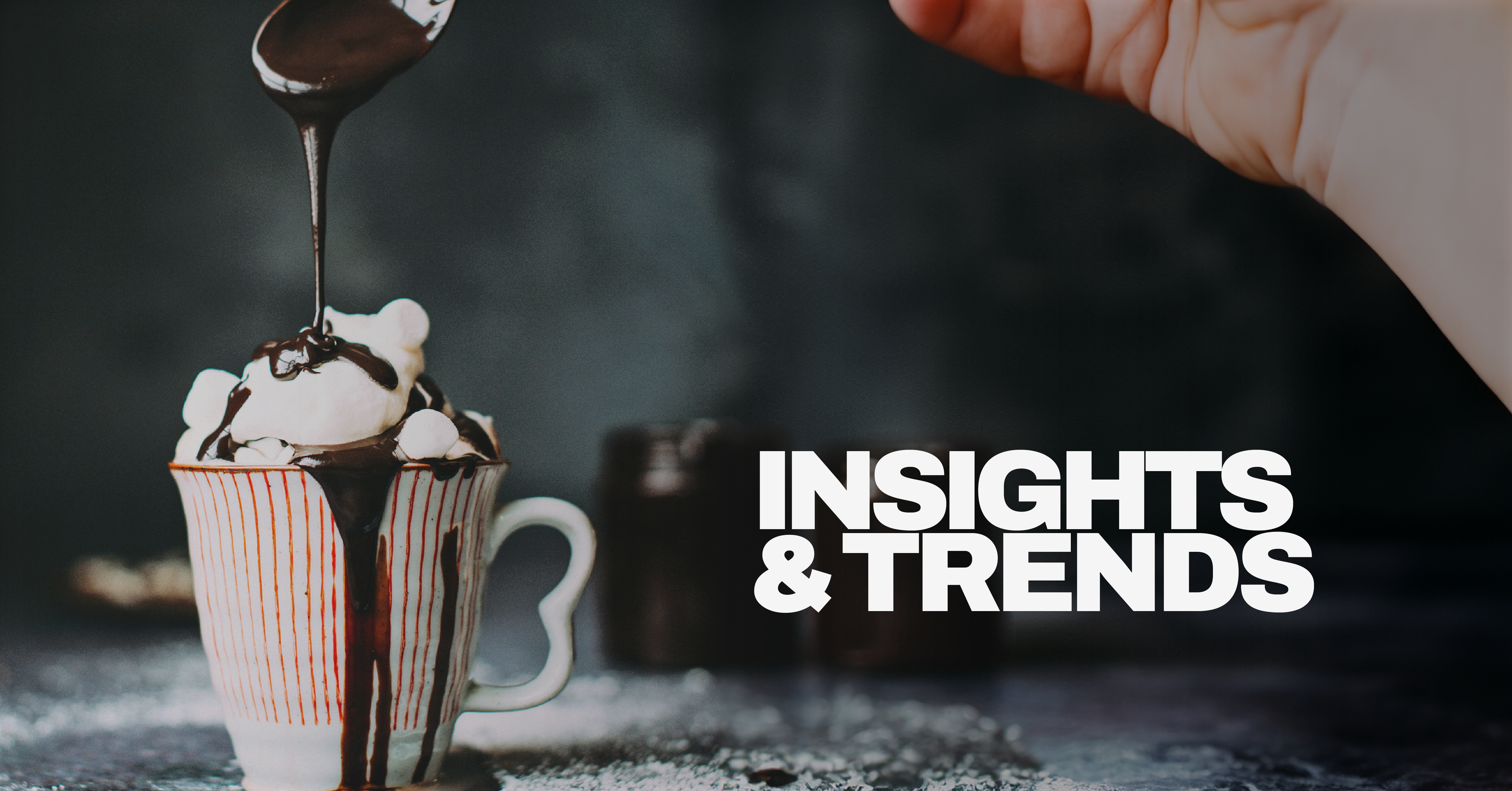
With winter on the way, it’s the perfect time to keep your Taylor equipment running strong by repurposing...
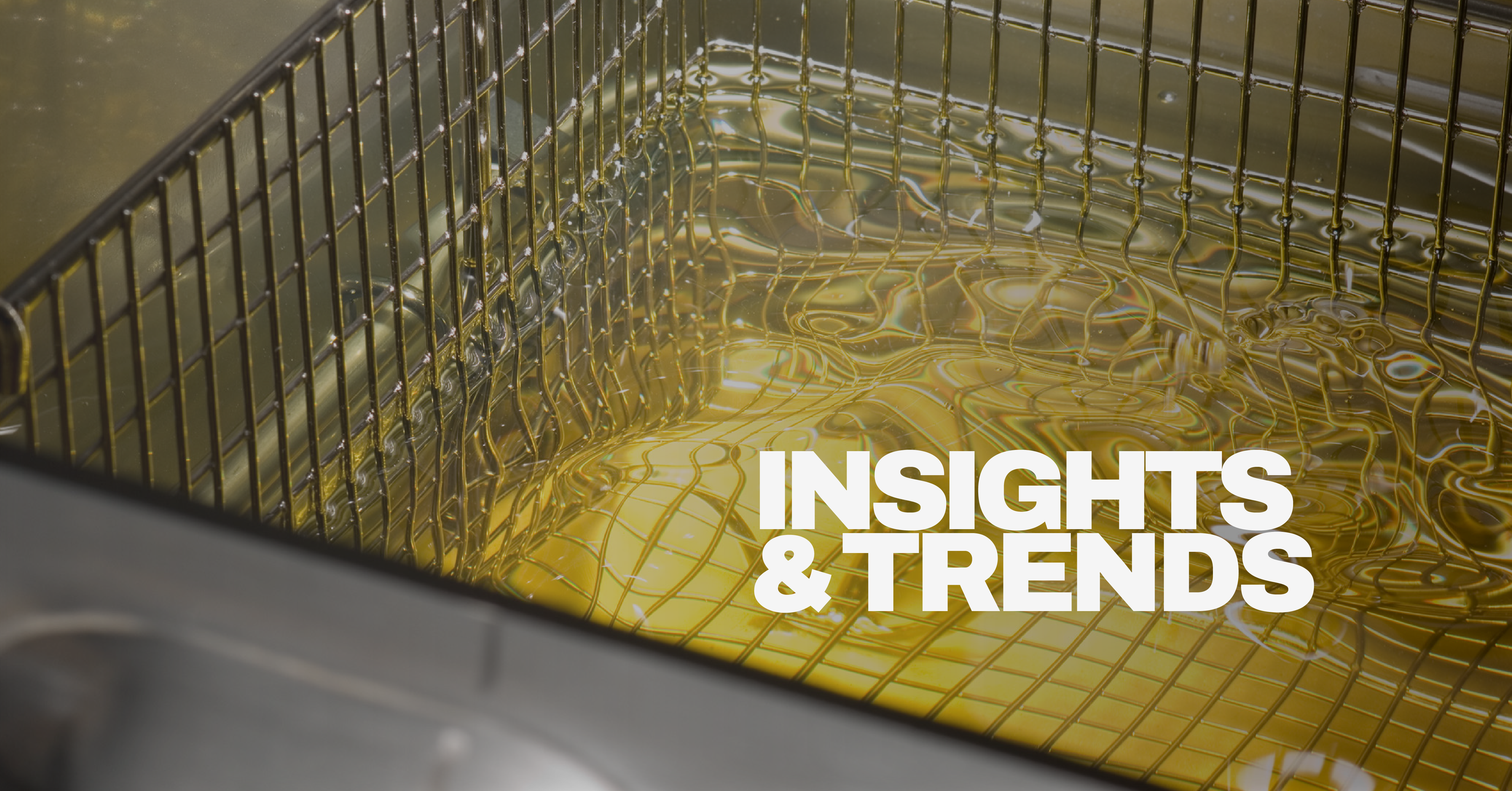
In the foodservice industry, where trends and tastes evolve quickly, one need remains constant: operators...
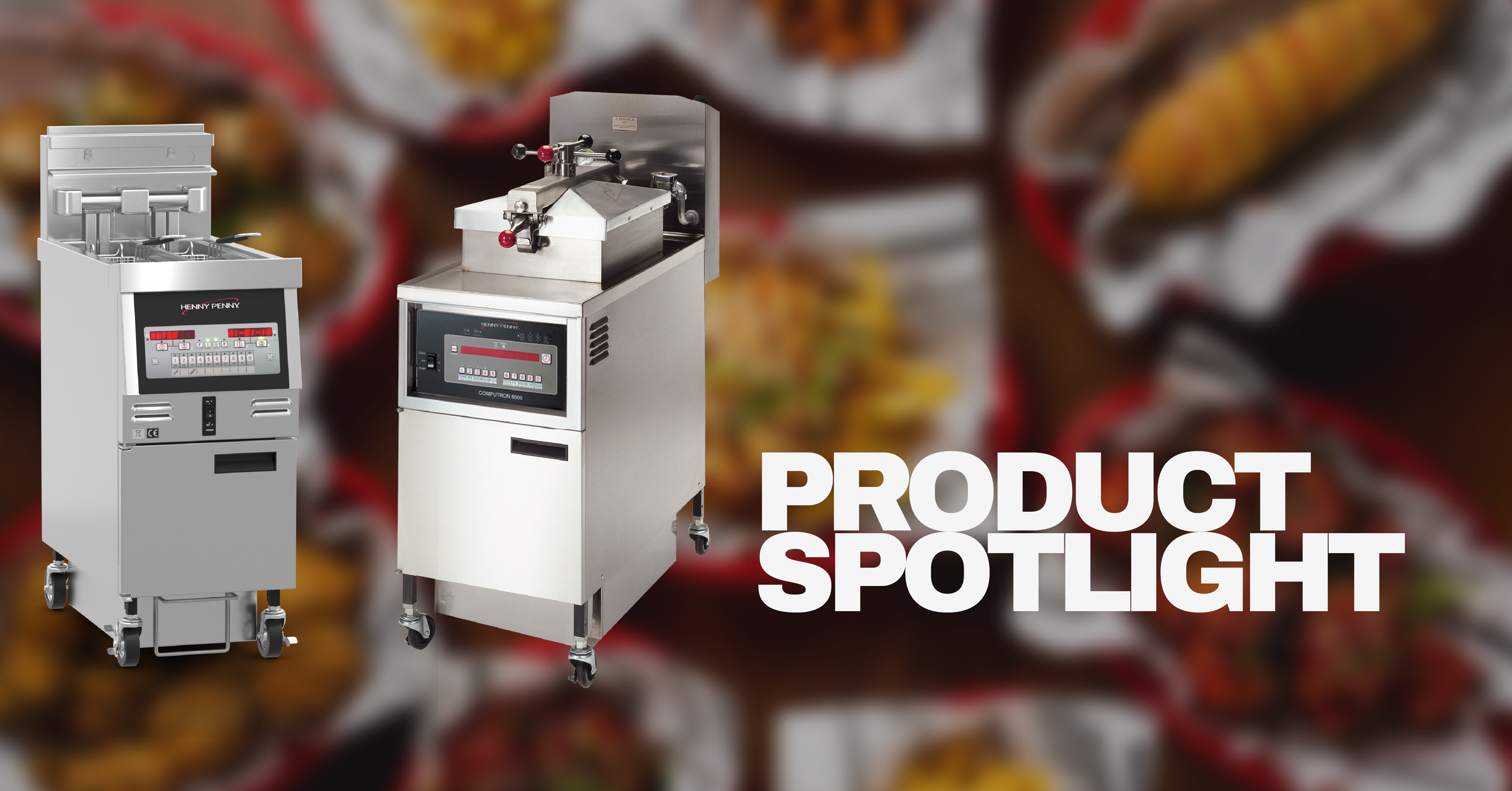
When it comes to frying, the method you choose can make a big difference in flavor, texture, and cooking...
No posts found
Load More
Loading...